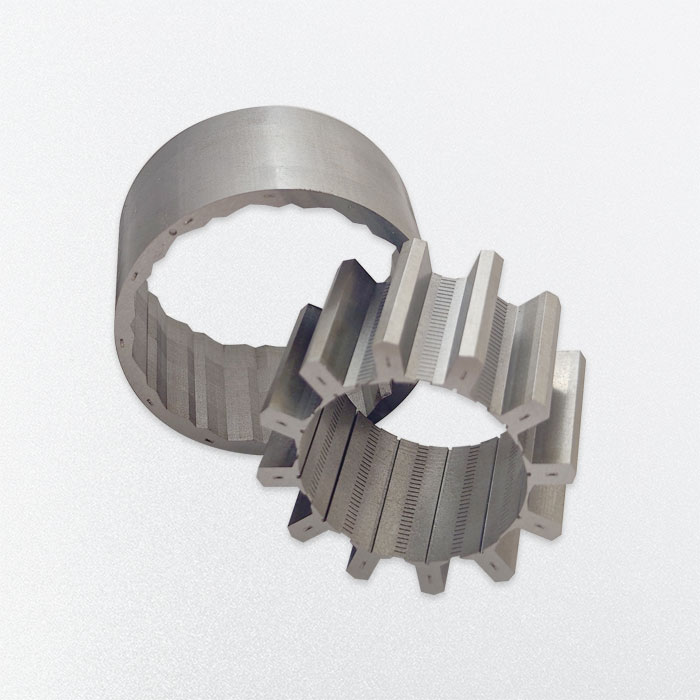
Stator & Rotor Lamination Stacks Manufacturer
- Lamination to stacking is crucial in core manufacturing, ensuring precise alignment, reduced eddy current losses, and optimal magnetic properties.
- We review the tolerances and offer design advice on the stator and rotor stacking process, based on the thickness of each piece, stack length, and overall design.
- Realize Batch Production of In-Mold Glue Dispensing
- Various Automatic Lines and Manual Stacking Processes
- 32 Sets Punching Machine From 80T~650T
- Customization for Diverse Applications
- Certificate: IATF16949
Our Stacking Processes
Stator and rotor stacks are assembled from laminations using methods like riveting, interlocking, welding, gluing, bolting, buckling, or self-adhesion (backlack). For longer laminations, two methods are often combined for stability.
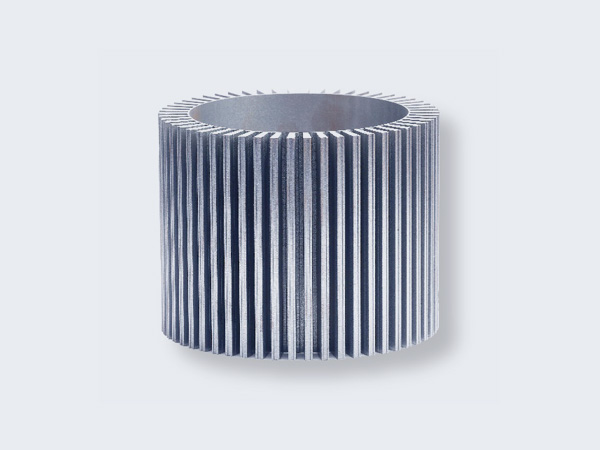
In-Mold Glue Dispensing
- Dispensing solution completed inside the mold.
- Glue solidifies within 10-20 seconds.
- High interchip strength.
- Excellent performance parameters.
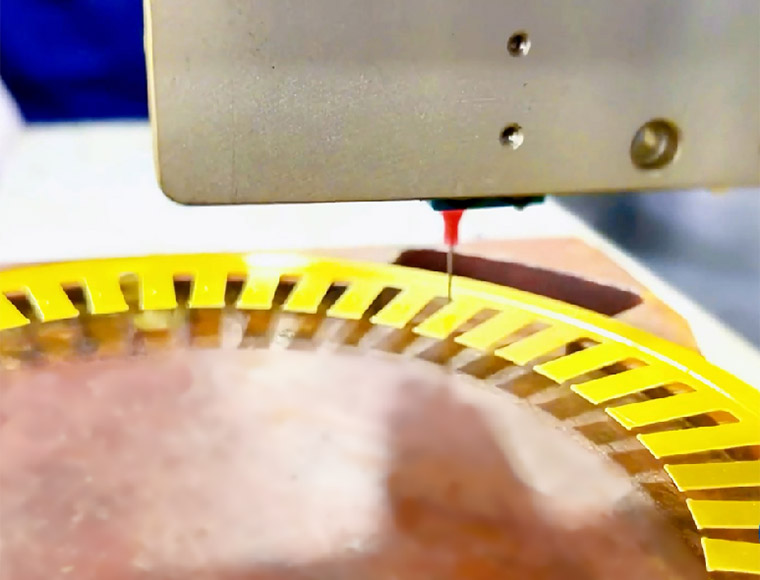
Out-Mold Glue Dispensing
- Applied outside the mold.
- Visual automatic positioning system combined with the injection valve needle cylinder dispensing.
- Tilt or 360-degree rotation dispensing.
- Self-adhesive coating heating scheme.
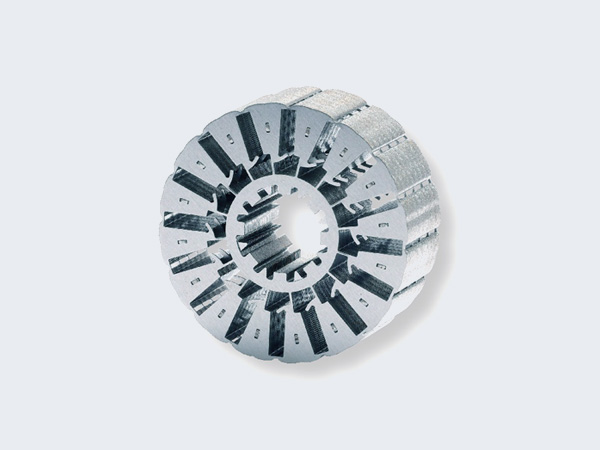
Progressive Mold Self-Interlocking Stacking
- Automatically completes interlocking during stamping.
- Efficient for high-volume production.
- Rectangular or round interlock points.
- Works for rotor and stator laminations.
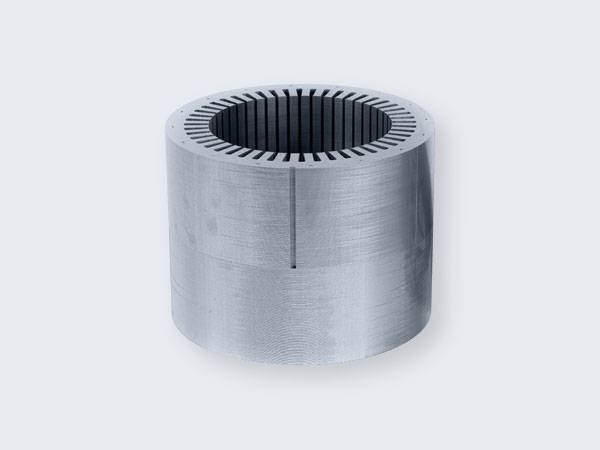
Compound Mold Single Punch Self- Interlocking Stacking
- Secures interlock at specific points.
- Ideal for smaller batches or customized parts verification.
- Flexible process with human intervention.
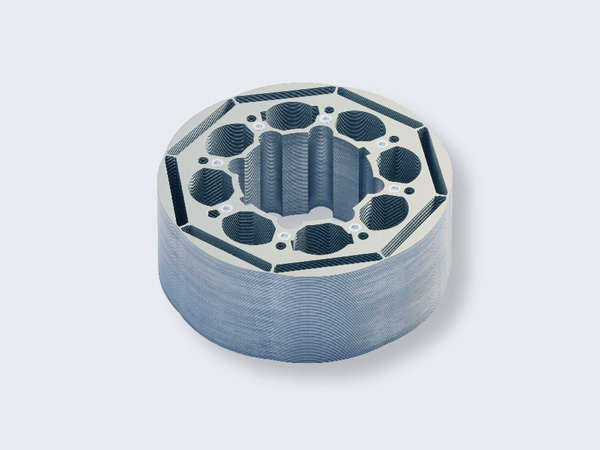
Rivet Stacking
- Use head or flat rivets.
- Ensures durable connection and secure assembly.
- Suitable for rotor laminations.
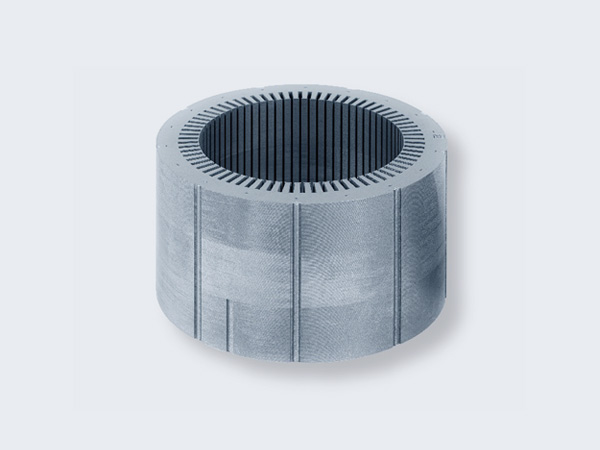
Welding Stacking
- Laser, TIG, galvanometer welding methods.
- Ensures strong bond, minimal distortion.
- Best for high precision stator laminations.
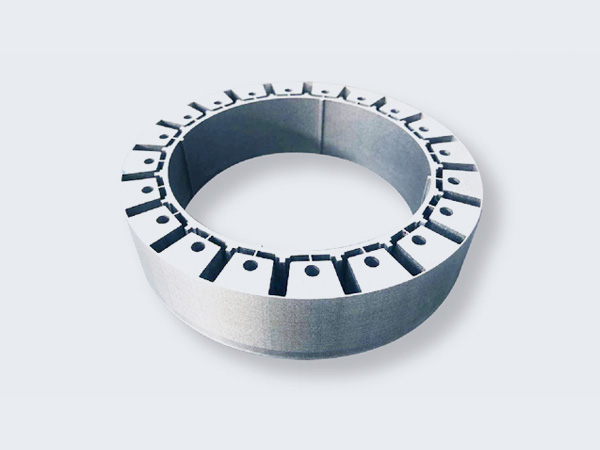
Self-Adhesive Stacking
- B35A300-Z/B50A400-Z etc. Heat Adhesives.
- Smooth finish, strong bonding, durable.
- Ideal for advanced heat-activated coatings.
- Works for rotor and stator laminations.
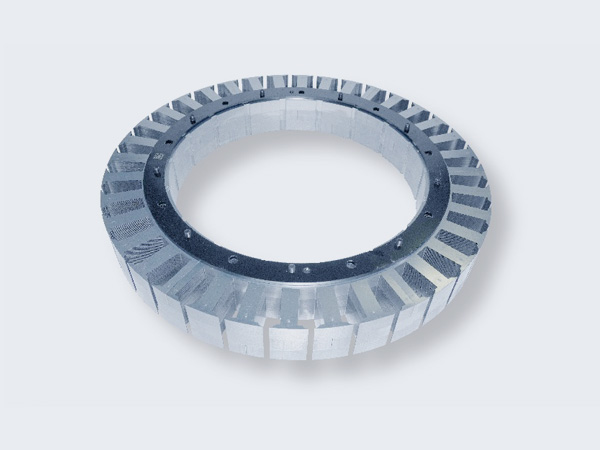
Bolt Stacking
- Assemble large-diameter stator laminations.
- Offers adjustability, stability, and reusability.
- Great for large motors with robust connections.
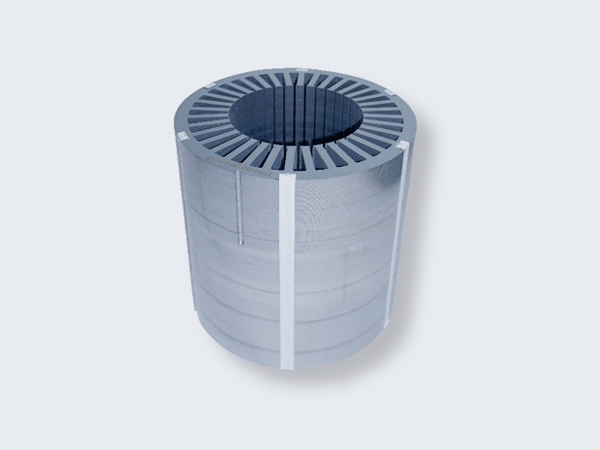
Buckle or Clamping Stacking
- Straight or oblique buckles.
- Quick assembly, robust design.
- Best for compact stator lamination.
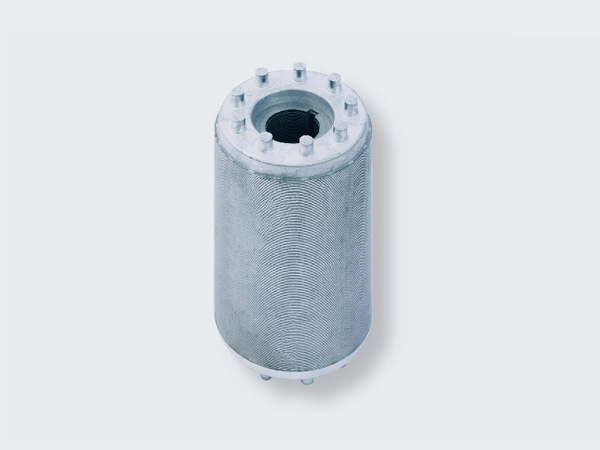
Al-casting or Cu-casting Stacking
- Both single lamination and stacking can be casting pressed.
- Equipped with horizontal and vertical aluminum casting equipment to meet different outer diameter and height requirements.
- Best for compact rotor lamination.
Our Common Motor Core Stacks
Our stator and rotor core stacks offer durable, application-specific solutions for DC, BLDC, and induction motors in both industrial and consumer settings.
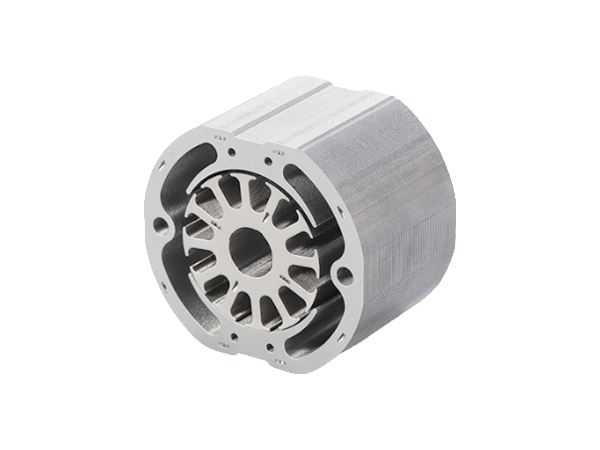
Induction Motor Core
- Slotted stator and squirrel cage rotor core for induction.
- Uses AC fields without permanent magnets.
- Used in pumps, compressors, elevators, and industry.
- Durable, cost-effective, and reliable under heavy load.
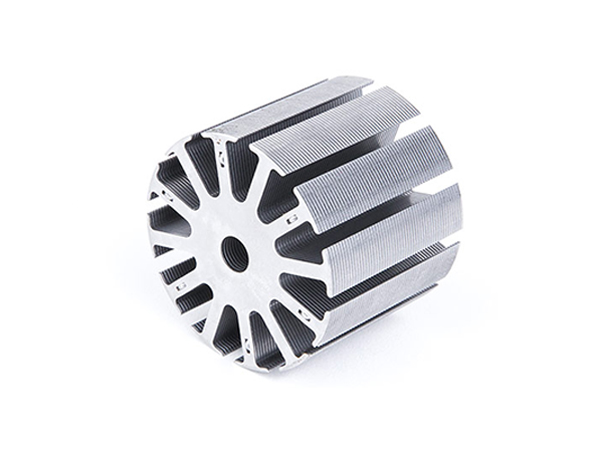
DC Motor Core
- Laminated stator core slots guide coil winding and magnetic flux.
- Supports brushed motors with direct torque and easy control.
- Commonly found in small home appliances, tools, and toys.
- Compact, affordable, and simple to manufacture.
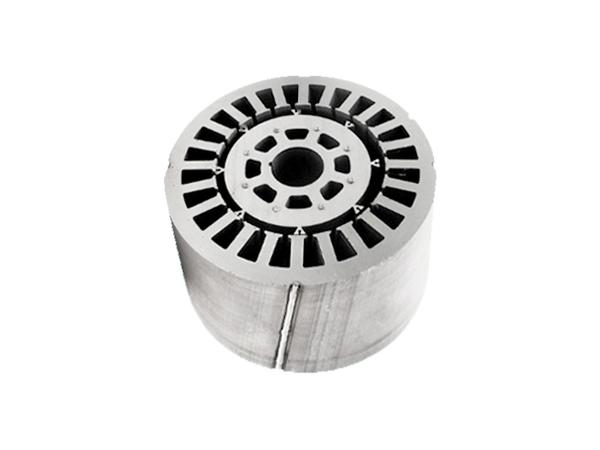
BLDC Motor Core
- Stator core enables electronic commutation and magnetic precision.
- Rotor core uses permanent magnets for torque and efficiency.
- Common in drones, e-bikes, and HVAC.
- Quiet, low-maintenance, and long-lasting performance.
Stacking Process Steps
After producing the stator and rotor laminations, the assembly and fixation of the stator and rotor stacks typically follow these nine common steps:
01. Prepare Laminations
02. Laminations Alignment
03. Selection Stacking Method
Choose interlocking, welding, bonding, or clamping methods based on design and performance requirements.
04. Stacking the Laminations
05. Compression and Clamping
06. Securing the Stack
07. Dimensional and Geometric Inspection
08. Post-Processing (Optional)
09. Final Quality Inspection
Conduct thorough electrical and mechanical checks to ensure the stator stack and rotor stack meet all functional and safety standards.
Post-Stacks Processing
We utilize various processes to enhance the structural integrity, performance, and longevity of laminated stator and rotor core stacks, ensuring optimal functionality.
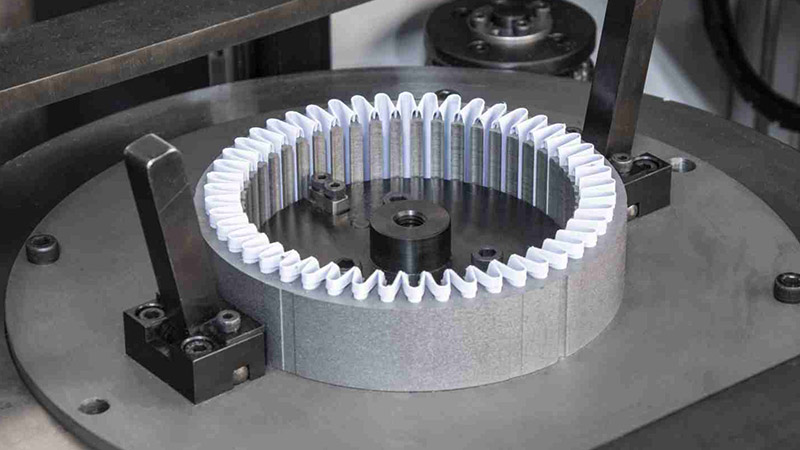
01. Insulation
02. Resin Curing
03. Plating Coating
04. Vibration Damping
05. Heat Treatment
06. Magnetic Treatment
07. Laser Marking
08. Surface Grinding or Polishing
Grinding wheels are used to remove rough edges and surface defects, improving the smoothness and finish of laminated stacks, enhancing efficiency and appearance.
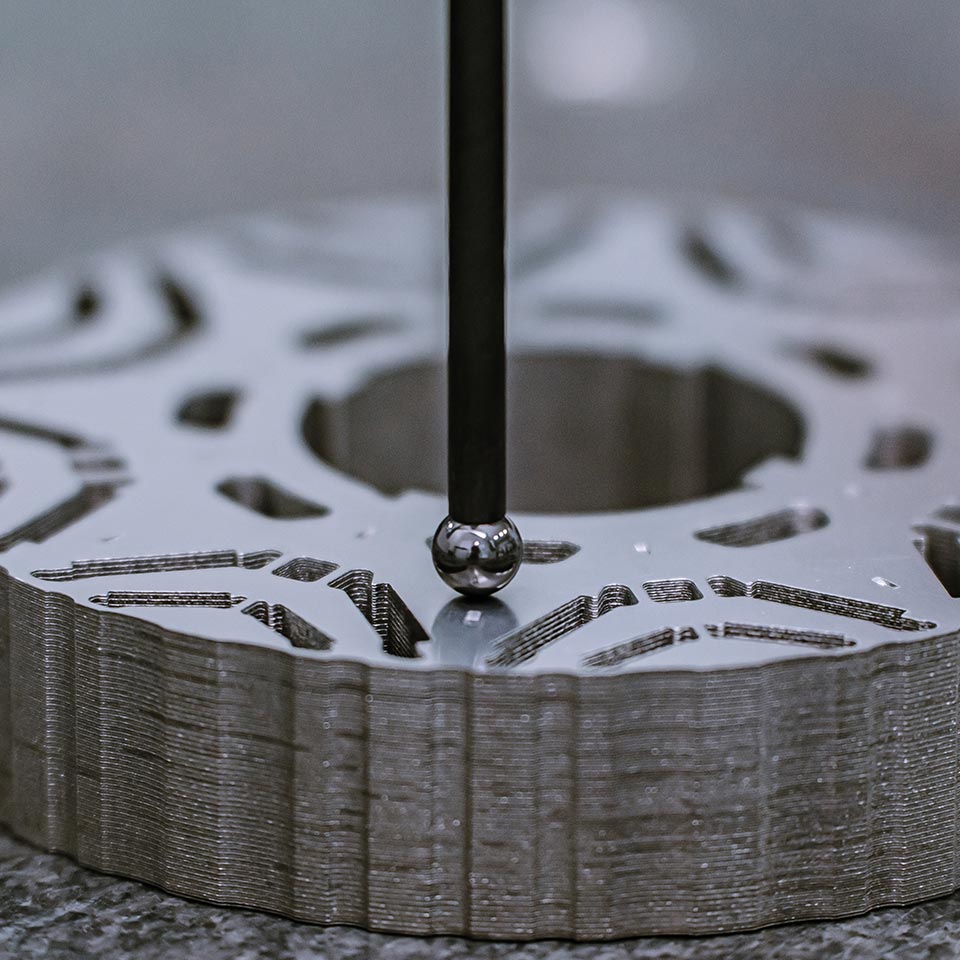
Final Quality Inspection
After post-processing, we conduct a comprehensive final quality inspection on our electric motor lamination stacks to ensure they meet all functional, safety, and performance standards.
- Visual Inspection
- Dimensional Measurement
- Magnetic Testing
- Electrical Insulation Testing
- Torque Testing
- Heat Resistance Test
- Vibration Test
- Mechanical Strength Testing
- Leakage Current Test
Customer Case
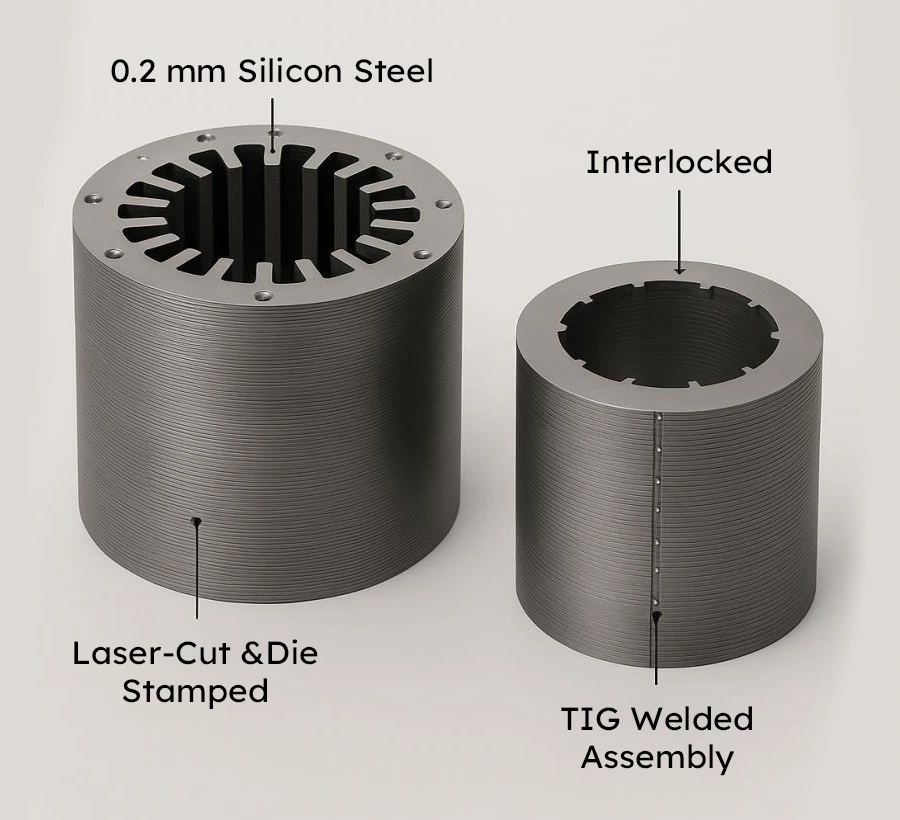
The Challenge
The client’s previous supplier was unable to meet performance and precision demands:
- Core loss was too high, impacting driving range.
- Stack concentricity and height variance caused imbalance and vibration
- Slow delivery timelines delayed product launch schedules
- They needed a manufacturer who could handle both development and long-term production.
Our Manufacturing Solution
We provided a fully customized stator & rotor stack solution:
- Used 0.2 mm high-grade silicon steel laminations for low loss.
- Applied laser-cutting and progressive die stamping to ensure accuracy.
- Delivered fully assembled stacks with interlocking and TIG welding.
- Enabled smooth transition from sample stage (50 sets) to mass production (20,000+ sets/month).
Result Comparison Table
Key Metric | Before (Previous Supplier) | After (With Our Solution) |
Core Loss @ 400Hz, 1.5T | 8.9 W/kg | 5.2 W/kg |
Stack Height Tolerance | ±0.20 mm | ±0.03 mm |
Rotor Concentricity Deviation | 0.12 mm | 0.02 mm |
Monthly Production Output | 5,000 sets | 20,000+ sets |
Prototyping Lead Time | 18 working days | 7 working days |
Assembly Defect Rate | 6.2% | 0.7% |